Лийн значи умно направено
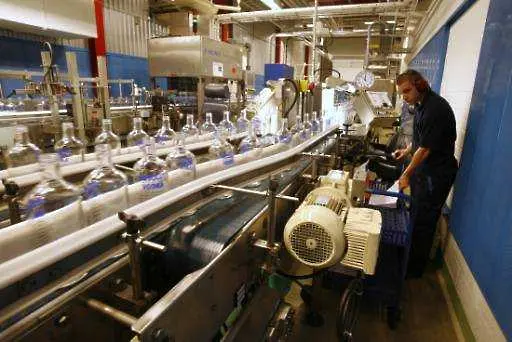
Лийн производството включва системата от техники за повишаване на ефективността, разработена е от големите японски компании през 80-те.
Тя се определя за третия етап в историческото развитие на индустрията, която от времето на занаятчиите преминава през ерата на масовото производство, за да достигне следващия етап, който съчетава най-доброто от двата предишни.
В една такава система работниците са организирани в екипи, като всеки един от членовете му има квалификацията да извърши сам всички задачи, възложени на екипа като цяло. Тези задачи, от своя страна, са по-специализирани в сравнение с работата, която се възлага на един работник при масовото производство. Това относително разнообразие позволява да се избегне съкрушителната монотонност на поточната линия в чистия й вид.
При лийн производството, отделните елементи и материали се доставят на работното място на всеки екип в точното време, когато следва да започне изработването на продукта. Всеки от работниците може да спре производството, ако открие дефект като това се насърчава.
Ето я най-съществената разлика в сравнение с класическия подход на поточната линия, при която спирането на производството е много скъпо и затова се прави само в краен случай, и то ако не може да бъде избегнато по никакъв друг начин.
Проблемът е, че работниците на поточната линия на практика не придобиват никакви допълнителни умения, не научават нищо ново. Това води до голямо количество дефектна продукция. Наетите нямат стимул да търсят причината за възникването на дефектите, нито имат право да вземат участие при отстраняването й, ако я открият.
Мениджърите се забелязали, че при първоначално въвеждане на лийн системата е нормално да се налага често спиране на производството, докато проблемите се открият и изгладят. Постепенно, обаче, има все по-малко причини за спиране и все по малко проблеми.
При лийн, дизайнерите работят в тясно сътрудничество с работниците и доставчиците. Има непрекъсната двупосочна комуникация. Проблемите се решават незабавно при откриването им, а производството се усъвършенства в процеса на работата.
Лийн производството – стъпка по стъпка
- Ръководството на компанията решава да намали разходите и да повиши качеството на производството.
- Определя ръководител на проекта, който представя идеята и целите на работниците.
- Набират се доброволци (до 7 души от различни отдели), които да съставят екипа, който ще организира прилагането на новата концепция.
- Прилага се обучение за техниките, присъщи на новата система.
- Насърчават се контактите и обмяната на опит с други компании, които не са директни конкуренти, и които вече прилагат лийн.
- Избира се пилотен проект – за отделен продукт или отдел.
- Намалява се обема на партидите и се контролира стриктно графика.
- Определя се колко точно материал е необходим и кога във времето да бъде доставен.
- Увеличава се честотата на вътрешните доставки (ако е възможно и на външните).
- Проследява се внимателно движението на елементите в целия производствен цикъл.
- Установява се кои са най-честите, видими проблеми с качеството и ритъма на производството.
- Два до три месеца след стартирането на пилотния проект се оценяват резултатите и се установява къде са допуснати грешки и защо?
- Постепенно се разширява обхвата на лийн системата в цялото производство.
- Регулярно се оценяват резултатите и се насърчава активна обратна връзка.
- Организират се редовни обучения в рамките на индустрията.
- Ако е нужно се отстраняват определени хора.
- Въвеждат се стандарти и се стабилизира ритъма на работата.
- Обобщават се постигнатите резултати и се търсят начини за постоянното подобряване на качеството.
- Лийн се превръща в обичайна практика, а възвращаемостта на инвестициите се повишава.
Ключови думи
ОЩЕ ОТ КАТЕГОРИЯТА
|
|
Коментари
Няма въведени кометари.